Laminate Flooring Manufacturing Process
Laminate flooring is the most popular flooring in the market because of its largest capacity and cheapest price. There is no raw materials limit for its production and it has vey even color and milling. Laminate flooring is easy maintenance, no complicated daily cleaning required, and it can be replaced quickly when it is damaged or old style. Laminate flooring is pressed by multi layers, including wear layer, balance layer, substrate etc.
- Wear-resistant paper: It is aluminum oxide, anti-scratch, to protect flooring surface without big and deep scratches and water not going into flooring. Paper is divided by the weight - 25 g, 38 g ( 4000 rolls ), 45 g ( 6000 rolls ) and 58 g.
- Print paper: The color of flooring will be printed on this paper.
- Substrate: It is high density fiberboard which is pressed from wood fiber with eco friendly and non toxic glue. The base has white core and green color. Green core is waterproof, in order to differ from white core, green color was made.
- Balance sheet: It could cause the board bending when pressing the wear-resistant paper and print paper. A balance sheet is required to balance the strength of 2 layers. Also, balance sheet is to prevent moisture goes up from the ground. Balance sheet is 33g, 45g, 90g and 110g in generally.
Laminate flooring grooves are: Square edge, V groove and Molded groove
- Square edge: Flooring will be extremely flat after installation, no gap. Easy to clean, no dust sticking inside of gap.
- V grooves: This is brand new grooves in laminate flooring and it looks like solid wood flooring with grooved edges. The biggest problem with V groove is the dust sticking inside of this gap. It need be waxed on the grooves after installation immediately.
Molded edges:
It is a patented technology. When pressing, the edges on flooring will be pressed into a U groove, it is better than V groove, V is too deep, U is shadow. So, U is easier in cleaning than V.
Laminate flooring process:
- Printing
- We select tress with decades and hundreds of years and cut it into pieces, then scan the most clear and beautiful piece as the final flooring color. We sculpture the scanned picture by laser machine to the printing roller and print it on the papers with imported ink.
- Printing ink is very important for the quality of paper. With strong ultraviolet radiation in 12 hours, color doesn't fade which can ensure laminate flooring will not fade in 7 years under sunshine.
- We have 3 printing line imported from Germany with capacity of 130 meters per second. It is really fast printing lines.
- Soaking into glue
- Printed paper, wear-resistant paper and balance sheet need be soaked into glue for pressing. Glue is eco friendly and no toxic. Glue is E1 standard, low VOC. It need have a strict control for soaking, otherwise, it could cause white spot on flooring, bending and cracks on wear-resistant paper.
- We have 10 soaking lines. Soaked paper also can be for the production of door, MDF board, computer desk, office furniture.
- Pressing
- After soaking, papers are ready for pressing and we need put them between two presser boards in sequence. The presser boards are stainless steel. The presser's temperature is 170-210 centigrade, pressure is 18-23 Mpa. Temperature and pressure will be adjusted by the paper weight.
- In pressing, we will make many types of laminate flooring, like. The different designs or grains are on the stainless steel presser boards.
- Presser in most of factories is 1400 tons and we have 8 pressers in 1800 tons and 2 pressers in 2400 tons.
- Shift on daytime can press 700 sheets and shift on night can press 800 sheets, so one day, 1500 sheets can be pressed.
Cutting the board: After pressing, we will cut the boards into 2 pieces or 3 pieces then cutting into flooring pieces.
Balance in condition room: The boards after cutting need fit the temperature and moisture in the factory. The flooring boards need stay in the conditioning room for 1 week in summer and 3-5 days in winter. Without balance, the laminate flooring boards will have the problems of bending, cupping and warping.
- Tongue and Groove:
- We manufacture Valinge glueless click system for laminate flooring in Homag machine which is imported Germany. Homag can run 130 meters per minute, most fast in the world.
- Square edge and molded edges flooring are the final product after Homag machine. For U or V grooves flooring, the edges will be sealed by lacquer.
Package: Final step is the packing. Laminate flooring will be packed by carton and pallet.
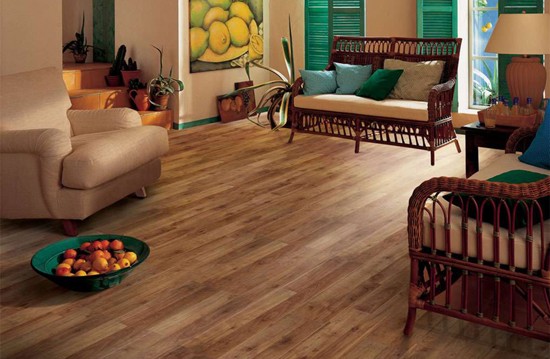