How is Bamboo Veneer Made
Bamboo veneer is getting very popular now in the market as bamboo is an eco-friendly and environmentally material rather than hardwood. Bamboo veneer has very natural color and is suitable for many modern designs, like hotel, museum, car.
People want to know how we can make the round and tall bamboo to be so soft and thin veneer. It must be an amazing process. Yes, it is. Bamboo veneer process is not a secret, but it is really complicated than regular wood veneer. We are glad to introduce the production of bamboo veneer and from this article, we belive you will get more specific information about our bamboo veneer.
There are 15 processing, please see them in the below photos and description.
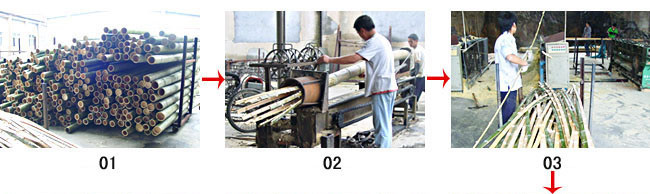
01 Cutting bamboo trees: After havesting bamboo from the mountain, bamboo need cut into the length of 2800mm to produce bamboo veneer.
02 Splitting bamboo trees to bamboo strips: 2800mm bamboo trunks need be splitted into small strips, round trunks can't be for the production.
03 Slicing bamboo strips into specific size: After splitting, bamboo strips are very rough, so need slice it to get a little smooth, not very.
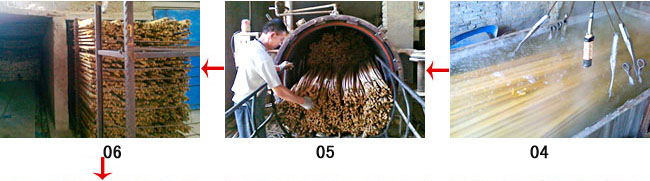
04 Boiling bamboo strips: Boiling is important for bamboo because boiling can get rid of sugar, starch and protein inside of bamboo, so insects can't survive any more.
05 Carbonizing bamboo strips: For carbonized color bamboo veneer, carbonizing is the must porcess. Carbonizing process is that bamboo strips are put inside of carbonizing tank in 4-6 hours with 200-300 centigrade.
06 Drying bamboo strips: After boiling, the moisture of bamboo is very high, drying will decrease the moisture. After drying, quality of bamboo veneer will be more stable, no bending.
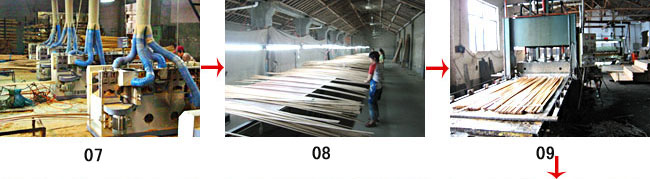
07 Slicing bamboo strips into specific size: Same as process step 3, now we slice bamboo strips very smooth, ready for next process step.
08 Sorting out bamboo strips: Bamboo is natural material, color variation is very big. We sort out bamboo strips by the color to make the color as even as possible, not 100% even, but we do the best.
09 Pressing bamboo strips together to get the block: Pressing is the key in the quality of bamboo veneer. Our presser is 800 tons and it is hot presser. This makes bamboo block better quality.
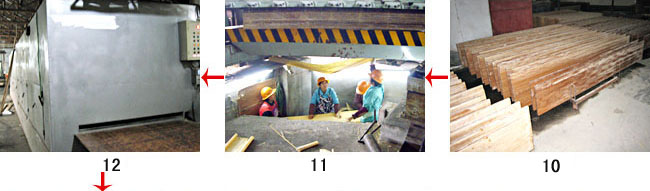
10 Soaking bamboo block: Bamboo block can't be sliced into veneer directly because it is too hard. Bamboo block is placed into a big water tank for 24 hours.
11 Slicing bamboo block into veneer: After bamboo block soaking into the water enough time, we slice it into veneer, slicing is very fast. After slicing, bamboo veneer is becoming a small roll, not flat.
12 Drying bamboo veneer: Bamboo block is soaking in the water for 1 day already, so moisture is very high, we need dry the veneer again to get a lower moisture content. Also, the veneer will become flat after drying.
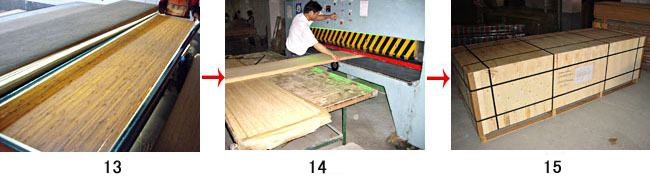
13 Quality checking of bamboo veneer: In slicing, there are some small defects on the veneer, so we need find them out and get fixed. We are pround to deliver 100% perfect veneer.
14 Cliping bamboo veneer: In the production, there are tolerance in length and width on the veneer, so we need cut the tolerance before packing to get the exact size as the customer orders.
15 Packing bamboo veneer: Bamboo veneer is packed by 100 pieces per carton, 40 cartons per pallet.