The Manufacture of Bamboo Flooring and its Types
The traditional method of making bamboo flooring is to slice the plant stalks into thin, flat planks. These can be colored in a particular color, varnished or untreated depending on the desired effect. These strips are then nailed to wooden beams or larger bamboo pieces to create a support system. Generally, the layout of the planks is relaxed, leaving irregular spaces in the floor. The conclusion is a floor that breathes, creation of a room that remains cooler and ventilated in the summer. It is the most common type of bamboo flooring used in Asia.
Bamboo parquet compressed
First, the stems of the bamboo plant are cut into thin strips so that they can be treated against vermin and insects. The material will be boiled and dipper in borax. The material is then mixed with fibers and adhesive. These fibers are pressed together in the form of blocks with the help of heat and pressure. Once the blocks are made, the material is reduced to usable floor sizes. It is then fully sanded and any finish is applied at this stage.
Solid bamboo flooring
This type of Bamboo flooring is made in a complex process that begins by slicing the stems of plants into strips of a specific measurement. The exterior skin is removed and the strips are boiled with boric acid to remove starch present in it. The material is then dried.
The natural color of bamboo is a light beige color but it can be obscured with the process of carbonization. This is where the raw material gets steamed using controlled pressure and heat that makes its surface darker and richer. Unfortunately, this process can also decrease the durability and hardness of bamboo. Whether charred or not, the bamboo slices are then oven dried.
The bamboo strips are then coated with adhesive resin and pressed together either horizontally, with the flat strips laid one on top of the other, or vertically, with the strips standing and pressed together on each side. The bound strands are subsequently pressed into thermal binders to dry the adhesive and join the disparate strands.
Engineered bamboo flooring
With engineered bamboo, the stems are also sliced, processed and glued together as is done for the solid bamboo flooring. However, once this operation is completed, the solid planks are cut into thin horizontal layers. These slices are then installed on a backing material such as plywood or fiber-board using heat, pressure and adhesive. Whatever the method applied, bamboo is not only a modern choice for your home but also environmentally friendly so do not hesitate!
Structure and formats of a bamboo parquet
For the creation of a parquet the stems of bamboo plants are cut into small rods, which are assembled together with glue or by pressing to form the floor structure; companies that build certified and durable parquets perform a particular process, that is they remove the bark and only use the central backbone because it is more resistant to gluing, to prevent the surface from flaking over time. Depending on the arrangement of the bars, there are three types of parquet:
• Horizontal: the rods are placed horizontally with respect to the supporting surface until they form more layers and the typical bamboo knots are highlighted;
• Vertical: the rods are positioned vertically with respect to the support surface, in this case, the knots are less visible, and the floor is composed of a single layer;
• Pressed: also called strand woven, in this type of parquet the rods are not glued, but pressed together, reaching a higher hardness than those with a horizontal or vertical structure.
As far as formats of bamboo flooring are concerned, three different types can be explored:
Solid wood: it consists of a horizontal, vertical or pressed plank, made entirely of first choice bamboo, with a thickness of 14 or 15 millimeters;
Prefinished or 2 layers : it is the most suitable to be laid on floor heating systems, the plank that composes it is formed by a visible layer of fine bamboo and by an underlying bamboo support of different species, placed transversally with respect to the noble layer, to give the parquet greater stability, the total thickness reaches 10 millimeters;
Multilayer: so called because underneath the visible bamboo layer of high quality and with a thickness of 4 mm, there is support formed by several layers of less precious bamboo or wood, to ensure maximum solidity.
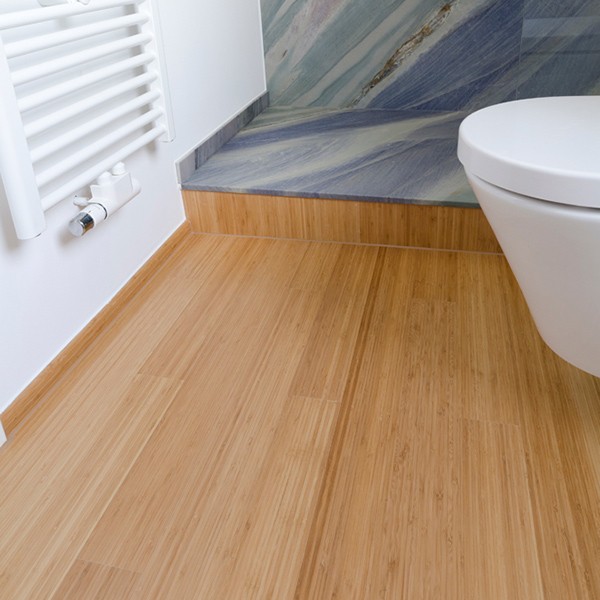